Design Control For Medical Devices
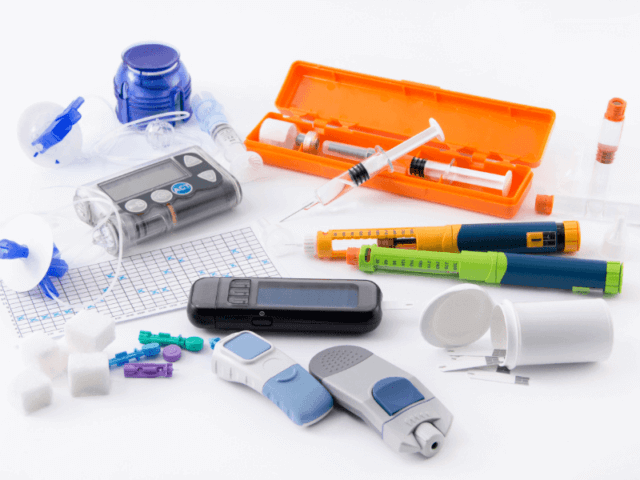
Design Controls For The Medical Device Industry
In the medical device industry, compliance with numerous requirements is well-known. Design controls are vital in a quality system that oversees a device’s lifespan, including requirements, development, production, distribution, use, maintenance, and obsolescence.
What are Design Controls?
Global regulatory agencies require proof of safety and effectiveness for your company’s medical devices. Meeting end-user needs, and requirements is crucial and falls under design controls.
Importance of Design Controls
Design controls are essential to guarantee that medical devices meet quality standards, perform as intended, and pose minimal risks to patients and users. By implementing robust design controls, manufacturers can proactively identify and mitigate potential issues throughout the development lifecycle. Design controls also help companies align with regulatory expectations and fulfill compliance requirements, such as those outlined by the U.S. Food and Drug Administration (FDA) or the European Union’s Medical Device Regulation (MDR).
Understanding Design Controls:
Regulatory Framework: Medical device manufacturers must adhere to various regulatory requirements depending on the jurisdiction they operate in. For example, in the United States, the Food and Drug Administration (FDA) outlines design control requirements in the Code of Federal Regulations (21 CFR 820.30). These regulations provide guidelines for design and development, design input and output, design verification and validation, design transfer, and design changes.
Key Elements of Design Controls: a. Design and Development Planning: Manufacturers should establish a comprehensive plan that outlines design inputs, design outputs, design reviews, and verification and validation activities. This plan should align with regulatory requirements and ensure that all stages of design and development are adequately addressed.
b. Design Inputs: This involves defining the intended use, user needs, and product requirements. Design inputs should be clear, measurable, and traceable, forming the foundation for subsequent design activities.
c. Design Outputs: Design outputs include specifications, drawings, and other documents that define the device’s physical and functional characteristics. These outputs should accurately reflect the design inputs and serve as a basis for verification and validation activities.
d. Design Verification and Validation: Verification confirms that the design outputs meet the design inputs and specifications. Validation, on the other hand, ensures that the device meets user needs and intended use within the defined operating environment. Both activities involve testing, analysis, and documentation to demonstrate compliance.
e. Design Transfer: Design transfer involves transferring the product design from the development phase to manufacturing. It requires careful documentation, training, and coordination to ensure a smooth transition while maintaining the integrity of the design.
f. Design Changes: Design changes may occur during the development or post-market phase. Manufacturers should establish robust change control processes to assess the impact of design changes, update documentation, and maintain regulatory compliance.
3.Documentation and Traceability: Thorough documentation is crucial for design controls. Manufacturers should maintain comprehensive records of design inputs, outputs, verification and validation activities, design changes, and risk management processes. These records facilitate traceability and enable effective communication among stakeholders, including regulators and customers.
Risk Management: Risk management is an essential aspect of design controls. Manufacturers should identify and assess potential risks associated with their devices throughout the design process. They should implement risk mitigation strategies, such as design changes, protective measures, or warnings, to minimize or eliminate risks to an acceptable level.