QMS Development and Support
Empowering Quality Excellence: Your Partner for QMS Development and Support
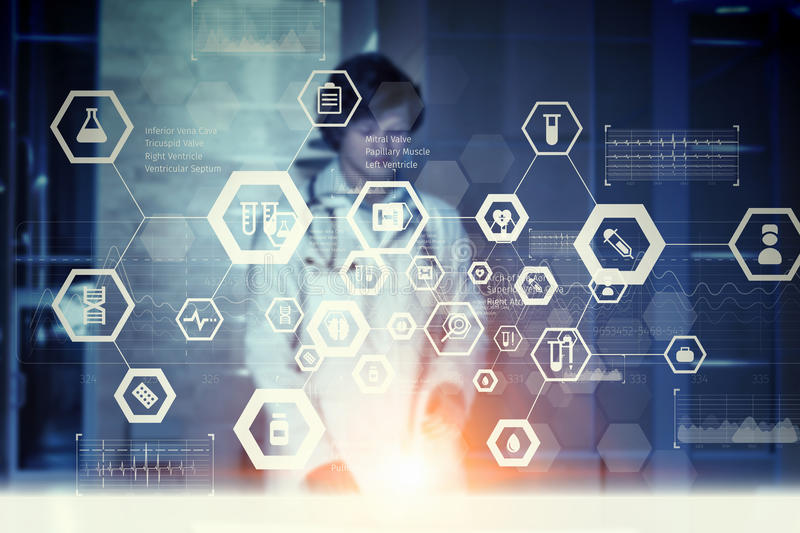
what is the purpose of a quality management system
QMS development involves designing a customised system that meets an organisation’s needs to plan, implement and monitor its quality objectives. The Quality Management System (QMS) documents an organisation’s processes, functions, and policies crucial for the continuous improvement of quality aimed to satisfy customer needs and expectations.
Medical Device Quality Management
A QMS for medical devices involves designing structured procedures and processes covering all aspects of the organisation’s operations, from manufacturing and procurement to supplier management, risk management, and systematically handling customer complaints.
The Medical Device Quality Management System is important because medical devices play a crucial role in the healthcare system by diagnosing, treating, and preventing various medical conditions.
Manufacturers of medical devices rely on quality systems as a vital tool to achieve high standards and provide optimal patient outcomes. QMS helps guarantee that its products meet the required standards and operate at peak performance, ensuring medical devices’ safety, effectiveness, and reliability.
what is iso 13485 standard?
International Organisation for Standardisation (ISO):13485 outlines the QMS requirements for medical devices, ensuring the safety and effectiveness of medical devices and protecting the health of users and patients.
ISO Quality Management System sets out criteria for a QMS in organisations engaged in all aspects of a medical device’s life cycle. Manufacturers around the globe widely recognise these standards and follow them.
Medical Device QMS Requirements
Medical devices must have quality management systems that fulfil certain requirements to meet regulatory standards.
These requirements are:
- Document Control
- Training Management
- Audit Management
- CAPA Management
Key Benefits of Medical Devices QMS
- Reduced market time for devices
Performing a thorough analysis of the underlying causes in the event of an error
Adaptability in compliance with industry regulations
Eradication of non-value added and waste activities
Improved supplier relations and management
The QMS Development and Support service helps organisations to do better, meet customer needs, and follow the rules and guidelines. When companies use this service, they can be sure that their quality processes work well, save time and money, and match their goals.
If you want a comprehensive QMS solution and support to manage quality processes more effectively, contact 3iConcept and talk to our experts.
Looking for QMS Consultant?
Let’s discuss your upcoming project.