QMS is a set of interconnected elements (Quality Policy, Procedures, Manual, Work Instruction, Records) that directs and controls the organization in consistently meeting customer requirements and enhancing their satisfaction.
What is quality management systems?
The quality Management System is a framework organizations use to ensure consistency in delivering products, services, and processes that satisfy or exceed customer expectations. The QMS is based on continuous improvement principles and encompasses a range of structured policies, processes, and procedures that ensure exceptional quality across all aspects of an organization.
It involves producing and managing documentation that specifies processes, roles, responsibilities, and rules while promoting an environment of accuracy and responsibility. Using a QMS, businesses can identify areas for improvement and take corrective and preventive actions when deviations occur. It helps them monitor, measure and manage performance in relation to quality objectives.
This systematic strategy to quality produces higher client satisfaction, easier processes, fewer mistakes, and an unwavering dedication to perfection. It also promotes supplier collaboration and risk management.
There are many types of Quality Management Systems (QMS) such as ISO 9001, ISO 13485, ISO 17025, ISO 14001, ISO/TS 16949, AS9100, TL 9000, Six Sigma, Lean, Capability Maturity Model Integration( CMMI), Good Manufacturing Practice (GMP) and Hazard Analysis and Critical Control Points (HACCP).
Elements of the quality management system.
As a structured framework, Quality Management Systems (QMS) allow organizations to ensure consistency in quality, continuous improvement, and customer satisfaction. This element includes:
Quality Policy and Objectives: The quality policy statement identifies how an organization is committed to quality. In this policy, the company outlines its commitment to meeting customer requirements and regulatory standards. The goal of improving quality is guided by measurable objectives.
Documentation: To specify, processes, methods, work instructions, and guidelines, thorough documentation is produced. This documentation enables tasks to be carried out consistently and ensures that staff members are aware of all requirements.
Process management: This is the process of identifying, defining, and recording important processes that have an effect on product or service quality. For efficiency and effectiveness, these procedures have been streamlined, standardized, and enhanced regularly.
Organizational Structure: There are clear definitions of the roles, responsibilities, and authorities connected to quality management. People will be more aware of how they can maintain and enhance quality as a result.
Risk management: Risk management involves identifying, evaluating, and managing potential risks that could have an impact on quality. To lessen or prevent these risks from influencing products, services, or tasks, strategies are developed.
Monitoring and measurement: To keep track of performance in relation to quality goals, the company establishes metrics, key performance indicators, and monitoring processes. Regular assessments help to discover errors and areas for improvement.
Corrective and Preventive Actions: When quality problems arise, immediate concerns are addressed through corrective actions. Preventive actions are also implemented to stop the occurrence of such issues.
Continuous Improvement: The company promotes a culture of constant improvement by frequently evaluating its processes, looking for potential opportunities for development, and making changes to increase both productivity and quality.
Now learn why Quality Management System is beneficial for the company.
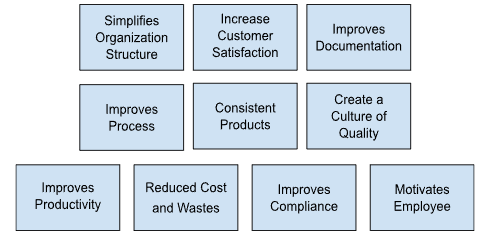
How to implement a QMS?
A Quality Management System (QMS) must be implemented in order to assure that the company’s procedures, products, and services continuously meet or surpass quality requirements. The general stages to implement a QMS are as follows:
Commitment from Top Management:
- Obtain the senior management’s commitment and support to secure the implementation’s access to resources, finance, and organizational support, get the senior management’s support and commitment.
Define the objectives and scope:
- Clearly state the divisions, processes, and activities that will fall under the QMS’s scope.
- Establish measurable quality goals that are in line with the larger objectives of the company.
Distribute Accountabilities:
- Assign roles and tasks for putting the QMS into practice and keeping it informed. To do this, a manager or coordinator for the QMS must be appointed.
Develop Documentation:
- Make new or updated documentation for guidelines, work instructions, processes, and procedures. Ensure that they are accurate, consistent, and aligned with the organization’s goals.
Training and Awareness:
- Train staff members about the QMS, its importance, and how it will affect their work. Ensure that everyone is aware of their role and duties within the QMS.
Process Mapping:
- The key processes of the company should be identified and mapped. Learn how processes interact and contribute to the final product or service.
Risk Assessment and Management:
- Identify potential risks that could have an impact on the quality of the product or service. Plan strategies for mitigating these risks and preventing their impact.
Monitoring and Measuring
- Establish metrics and key performance indicators(KPIs) to monitor the efficiency of your processes and the quality of your output. Establish techniques for data collection and analysis.
Conclusion
In the end, a Quality Management System (QMS) is the foundation of continual excellence across industries, to sum up. QMS provides flexibility with a variety of kinds focused on certain industries, from the flexibility of ISO 9001 to the medical device focus of ISO 13485’s medical device concentration, QMS provides flexibility. Its important elements include process documentation, risk management, constant enhancement, build a comprehensive framework for achieving the best quality. The success of a company over the long term relies on establishing a QMS, which requires commitment, process mapping, training, and common audits. Using a QMS can help businesses establish a culture of quality, customer satisfaction, and growth laying the foundation for long-term success.